مواد اولیه
مواد اولیه مورد نیاز جهت ساخت پیچ، مهره ، انکر بولت و قطعات قید و بستی شامل میلگرد و Rod می باشد که مواد پایه آنها با توجه به استانداردهای متریالی تهیه می شود. این مواد می تواند شامل فولادهای کم کربن، کربن متوسط، فولادهای آلیاژی، فولادهای نسوز، فولادهای ساختمانی، فولاد ابزار، انواع فولادهای زنگ نزن، آلیاژهای آلومینیوم، مس، برنج، مونل، سوپر آلیاژ های پایه آهن، نیکل و کبالت و غیره می باشد.
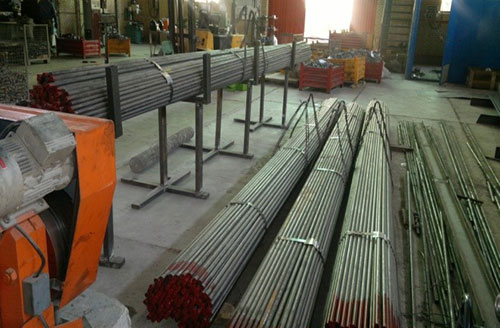
مهره مورد استفاده برای هر کدام از استانداردها بصورت پیشنهادی در بخش مشخصات فنی و استانداردها ارائه شده است. قابل ذکر است در اغلب موارد جنس مواد اولیه جهت ساخت مهره از جنس خود پیچ می¬باشد و اختلاف ترکیب شیمیایی آن از مواد اولیه مورد نیاز پیچ بسیار ناچیز است اما خواص مکانیکی مهره¬ها مانند سختی، استحکام تحت بارگواه تا حدودی متفاوت است.

فورج گرم
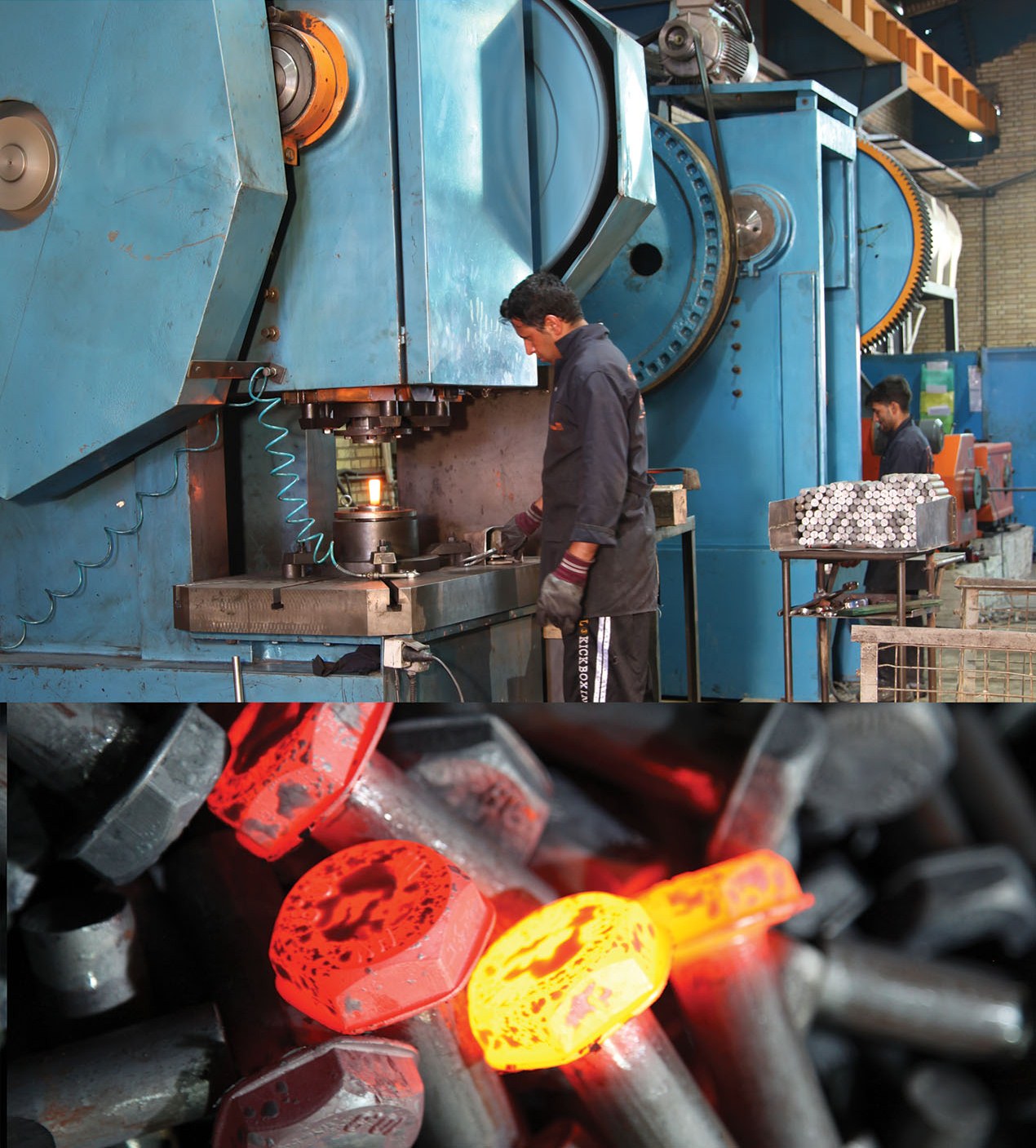
فورج گرم یکی از عمده ترین و عمومی¬ترین فرایندهای شکل دهی قطعات می باشد که از دیرباز برای تولید گل پیچ، مهره شش و هشت پر، انواع واشر خاص، قطعات شکل دار که برای تولید آنها، فورج یک مرحله اساسی و جزء مراحل استاندارد می باشد تلقی می شود. به منظور فورج گرم الزاماتی از قبیل پیش گرم و گرمایش قطعه تا دمای کارگرم و یا آنیل باید یک محدوده دمای مورد نظر و مجاز در استاندارد ساخت قطعات لحاظ شود. روش های گرمایش جهت پیشگرم و آنیل موضعی و کامل قطعات باید با توجه به حساسیت قطعات، عدم کربن زدایی سطحی، عدم ایجاد شیب حرارتی بسیار زیاد و الزامات استانداردهای قطعات انتخاب و انجام شوند. میزان طول مورد نیاز جهت محاسبه گل پیچ در هر سایز با استفاده از نرم افزارهای طراحی مهندسی و همچنین بصورت تجربی قابل دستیابی است. قابل ذکر است هر نوع و سایز برای پیچ ها دارای قالب های مجزا است که روی آنها علائم مارکینگ، برند تجاری سازنده و احتمالاً مشخصات پروژه ای که سفارش تولید داده شده است وجود دارد. البته فورج کردن قبل یا بعد از عملیات رزوه کردن می¬تواند انجام شود. فورج گرم با دو روش گل از بالا و گل از پایین قابل اجرا است که هر کدام دارای مزایای خاص خود است.


فورج سرد
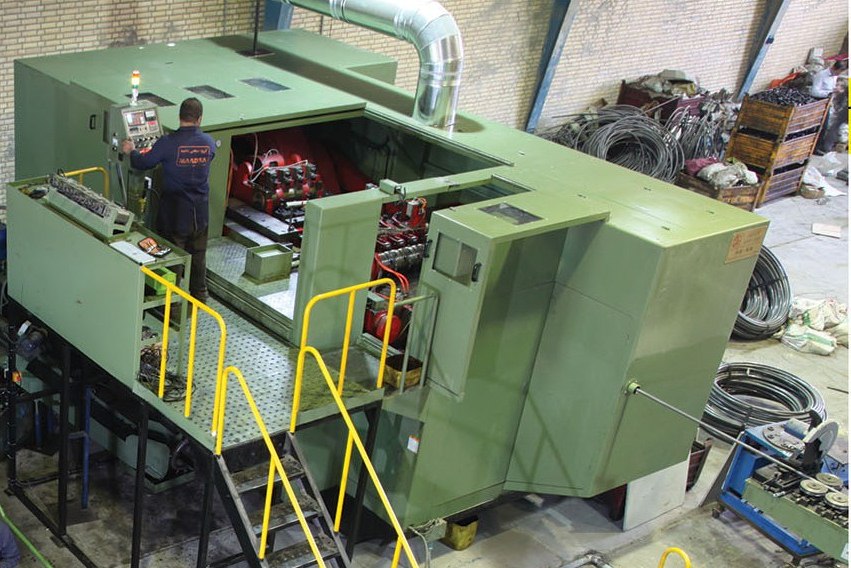
فورج سرد عموماً برای تغییر شکل های بسیار محدود با میزان کرنش و سرعت کرنش پایین و یا ورق های نازک و یا بسیاری مواردی که در چند مرحله قرار است شکل دهی شوند مناسب است. عموماً تولید پیچ و مهره با روش فورج سرد نیاز به مواد اولیه با تلورانس ابعادی دقیق، کیفیت سطحی بالا و قالب های مستحکم عموماً کاربید تنگستنی که هزینه آنها بسیار بالا است، اما از مهم¬ترین مزایای تولید به روش فورج سرد سرعت و دقت بالای تولید و افزایش میزان تناژ تولید می باشد. به ویژه برای پیچ های با سایز کمتر از 30 میلیمتر روش فورج سرد مناسب به نظر می رسد. قابل ذکر است، دستگاه های فورج سرد اغلب بصورت 1 تا 6 قالبه و بصورت نیمه یا تمام اتوماتیک موجود اند و کارکرد ساده ای دارند.

انبار محصولات
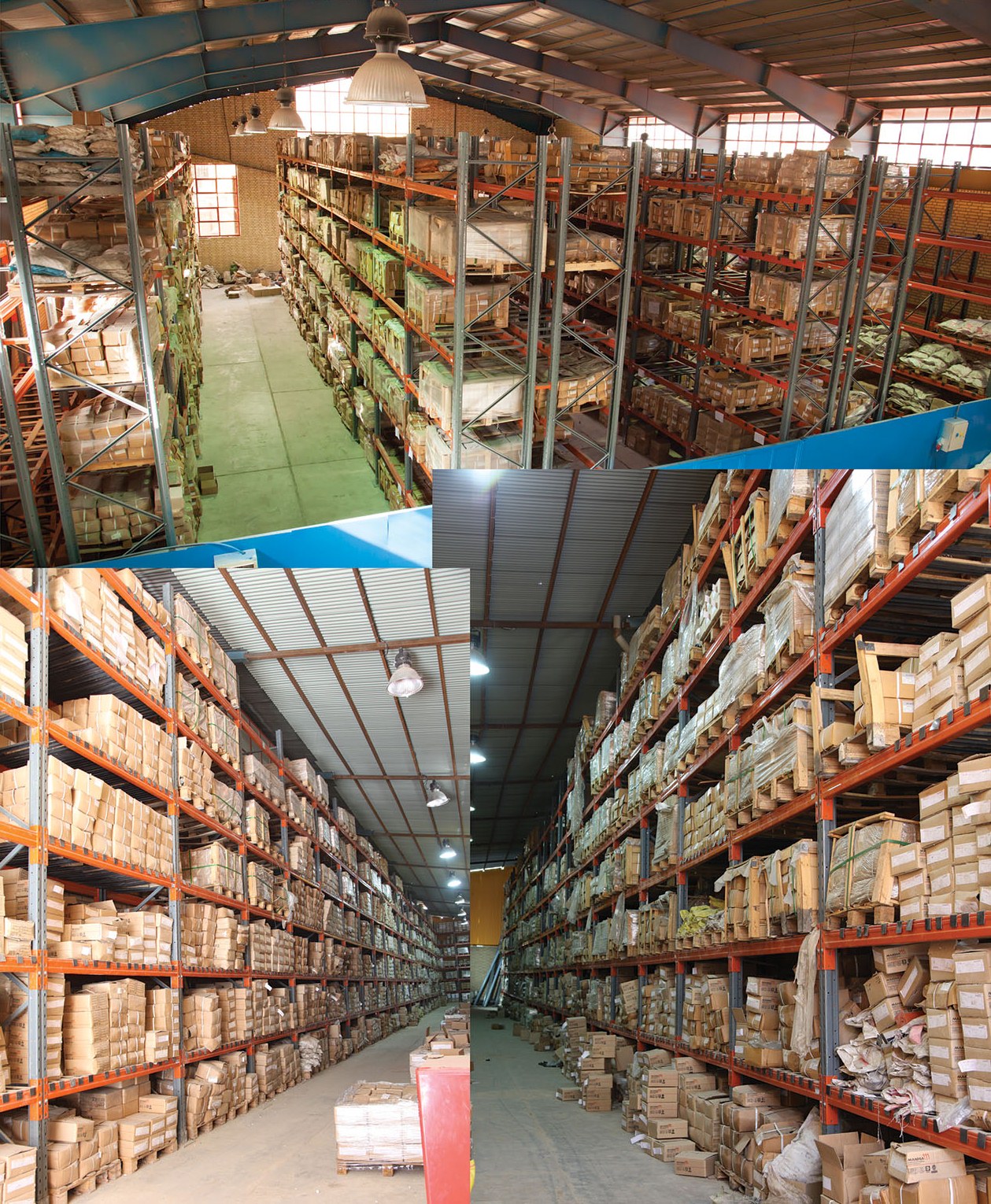
تولید انکر بولت
به منظور انواع مختلف انکر بولت، یو بولت، J بولت، Eye بولت و بسیاری اقلام قید و بستی که نیاز به خم کاری و شکل دهی دارند از دستگاه های خاصی استفاده می شود. برای این منظور در صورتی که فولاد در مقابل خم کاری مقاومت زیادی نشان ندهد و بخصوص برای سایزهای کوچک از روش سرد و برای سایزهای بزرگ تر یا فولادهای با استحکام بالاتر از روش گرمایش به روش القایی، شعله ای یا مقاومتی می توان استفاده نمود. این عملیات می تواند قبل یا پس از رزوه کردن انجام شود اما باید بعد از عملیات سایز کردن محل رزوه باشد زیرا پس از شکل دهی امکان سایزکردن بسیار محدود می شود. برای خمکاری با انواع شکل ها و زوایای مختلف از 30 تا 270 درجه نیاز به شابلون و مهارت خاصی است. اما مهم ترین خم ها شامل خم 90 و 180 درجه ای برای تولید L بولت و U یا J بولت است.
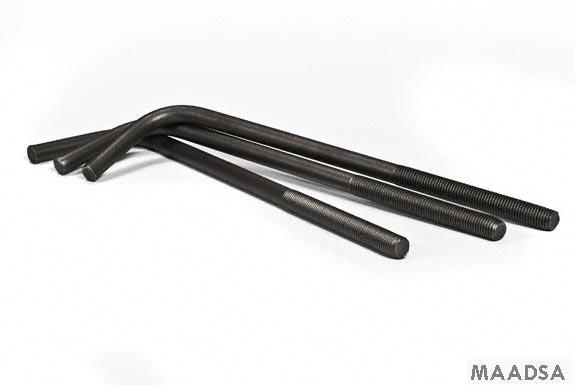



یخ زدن
پخ¬زدن یا Beveling یکی از موارد کلیدی است که اصولاً به دلیل فرایند¬های بعدی جهت رزوه ¬کردن و همچنین ایجاد یک شیب ملایم در ابتدای پیچ و مهره انجام می¬شود تا مهره به راحتی به پیچ بسته شود. از انواع روش¬ها جهت پخ زدن مناسب می¬توان برای پیچ و مهره¬ها و یا اقلامی که نیاز به پخ زدن قبل یا بعد از رزوه کردن دارند استفاده نمود که از جمله استفاده از وایرکات، فورج، تراشکاری با روش¬های مختلف و غیره را می¬توان نام برد.
رولينگ يا رزوه زني:
رولینگ یکی از حساس¬ترین قسمت¬های تولید یک پیچ است. برای رزوه زنی چندین روش وجود دارد که می¬توان از روش تراشکاری، استفاده از حدیده و قلاویز، استفاده از روش رولینگ غلطکی، اکستروژن و روش رولینگ اصطکاکی را نام برد. هرکدام از روش¬های نام¬برده مزایای خاص خود را دارند و برای تولید انبوه پیچ¬ها عموماً از روشی استفاده می¬شود که سرعت و دقت قابل قبولی داشته باشد. یکی از عمده¬ترین روش¬ها که در تولید انبوه مورد استفاده قرار می¬گیرد روش رولینگ دوتوپی و سه توپی است که هر کدام برای تولید قطعات و اقلام خاصی مورد استفاده قرار می¬گیرند. به طور مختصر می¬توان گفت که روش رولینگ دوتوپی برای تولید انواع پیچ¬های با گل شش گوش، مربعی، هشت پر، انواع آلن، پیچ¬¬های اتاقی، استادبولت و غیره مورد استفاده قرار می¬گیرد. روش سه توپی نیز برای اقلام فوق می¬تواند مورد استفاده باشد. رولینگ اصطکاکی برای تولید انواع رزوه¬های خودکار، پیچ¬های با انتهای هزار خواره، پیچ¬های با زروه متقاطع و رزوه با تلرانس لقی بسیار دقیق می¬تواند استفاده شود. در کل چارت گام رزوه مطابق با استاندارد رزوه مورد نظر برای هر نوع پیچ و مهره و استادبولت یا پیچ خودکار در استانداردهای مربطوه تعریف شده است که از آنها می¬توان برای تعیین گام رزوه، میزان زیرکار رزوه، میزان تلرانس لقی قابل قبول و همچنین تطبیق گام رزوه استفاده نمود. برای آشنایی بسیار مفصل و تکمیلی با مبحث انواع استانداردهای رزوه و انواع رزوه به Machinery’s Handbook مراجعه شود.

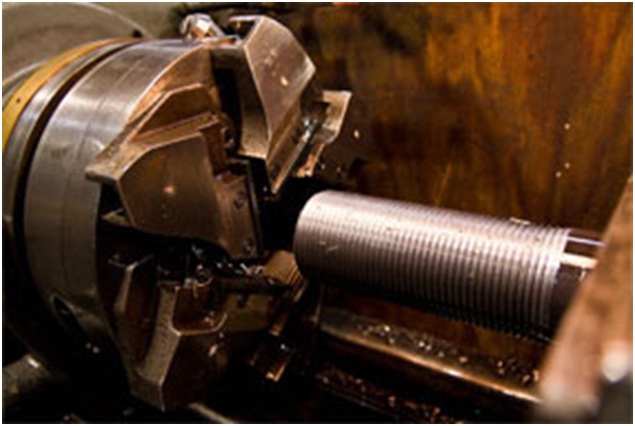
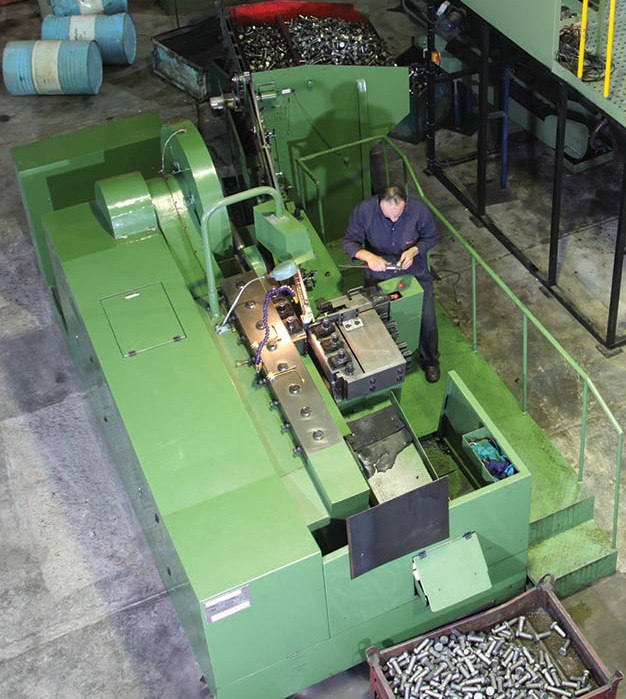
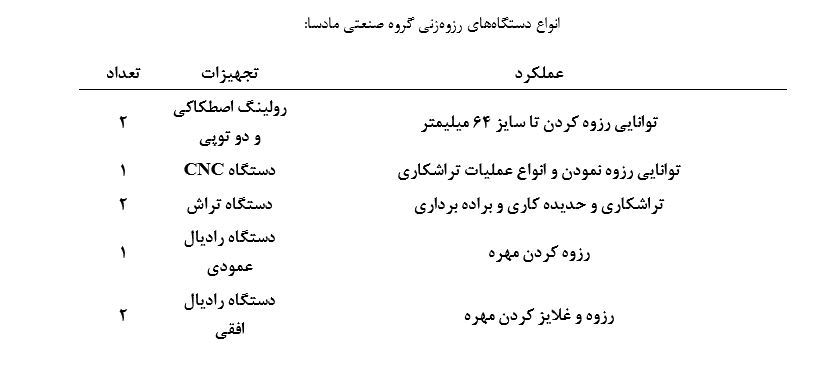
عملیات حرارتی
عملیات حرارتی یا به اصطلاح سختکاری پیچ، مهره، واشر، انکر بولت و تمامی اقلام قید و بستی بر اساس یک مبنای علم متالورژی و به منظور افزایش استحکام و سختی فولادها و آلیاژهای سختی پذیر، در مقابل تحمل فشار، کشش، برش و پیچش انجام می شود. در اینجا عملیات سختکاری در سه مرحله اصلی انجام می شود که عبارتند از:
- عملیات پیش¬گرم و گرمایش (حرارت دادن تا بالاتر از محدوده دمایی آنیل)
- سرمایش سریع در آب، آب نمک، آب- روغن، روغن یا هوا
- گرمایش مجدد به منظور بازگشت سختی و استحکام تا حد مورد نیاز (تمپر کردن)
قابل ذکر است هر فولاد یا آلیاژ سختی دارای یک منحنی T-T-T یا C-C-T است که بر اساس آن تنها در شرایط خاصی می توان به حداکثر و حداقل تغییرات سختی و تولید مارتنزیت دست یافت و به این لحاظ هر فولاد باید با یک سرعت خاص و در یک محیط سرد کننده خاص سرد شود تا میزان مارتنزیت و فازهای سخت و پراستحکام در آنها بوجود آید. ایجاد یک ساختار پر استحکام با کوئنچ کردن قابل حصول است اما این ساختار تُرد است و باید به منظور افزایش انعطاف پذیری در دمای مشخص زیر دمای یوتکتوئید فولاد حرارت دهی مجدد انجام شود تا سختی و استحکام و انعطاف پذیری فولاد به موازنه درآیند و خواص استحکامی فولاد بر اساس استاندارد مرجع آن حاصل شود. در سیستم های قدیمی عملیات آنیل،کوئنچ و تمپر در سه وان حمام نمک، کوره¬های عمودی و یا کوره های افقی انجام می شد که با انرژی سوخت فسیلی، مازوت و یا روش های سنتی کار می کردند. پس از استفاده از انرژی الکتریکی و پیشرفت های اخیر کوره های الکتریکی جای سوخت های قدیمی را گرفته و به تدریج کوره های عملیات حرارتی پیوسته (Continuous Heat Treatment Furnace) جایگزین تمامی روش های سنتی شد.
سیکل عملیات حرارتی در کوره های پیوسته شامل یک کوره آنیل (پخت) ، یک حمام کوئنچ پس از آنیل و یک کوره بازگشت می باشد، البته قبل از آنیل و همچنین قبل از بازگشت دو حمام چربی شویی نیز وجود دارد و در نهایت نیز یک حمام سیاه کاری وجود دارد که پیچ های تولید شده به منظور ممانعت در مقابل خوردگی در هوا تا مدت زمان کوتاهی حین انبار اعمال می شود.
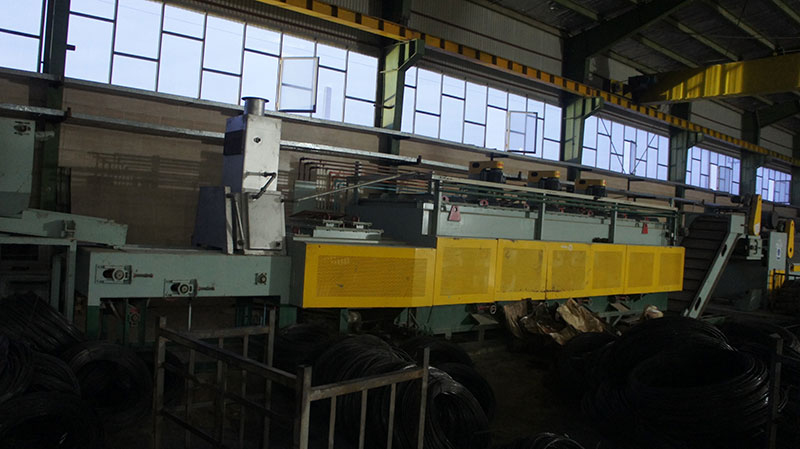
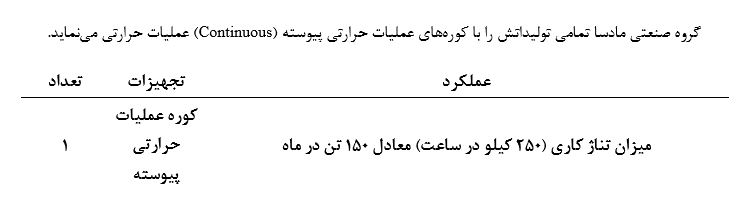
عملیات پوشش دهی
عملیات پوشش دهی قبل از بسته بندی و ارسال مرحله نهایی تولید می باشد. البته همه انواع پیچ و مهره و واشر مجاز به هر نوع پوشش دهی نیستند؛ مثلاً فولادهای بسیار مستحکم و پرمقاومت اکیداً توصیه شده است که نباید گالوانیزه گرم شوند.
عملیات پوشش دهی با انواع روش های مختلف قابل اعمال است که از جمله می توان پوشش دهی مکانیکی، پوشش ذوبی، پوشش الکترولیتیکی ، پوشش های آندایزینگ، پوشش پلیمری، پوشش پلاسما اسپری و غیره را نام برد. اینها روش های اعمال پوشش هستند. پوشش های مختلفی که شرکت مادسا می¬تواند روی قطعات مختلف پیچ و مهره اعمال نماید شامل موارد ذیل است:
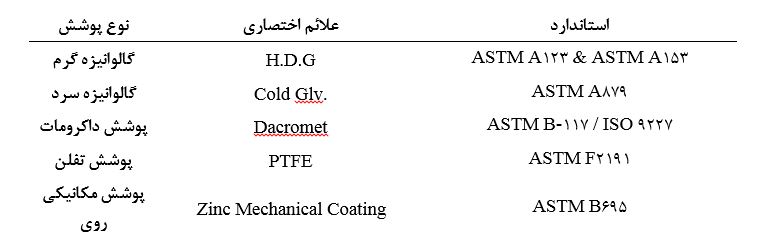
هر کدام از پوشش های مختلف مذکور الزامات خاصی دارند که از جمله مقاومت در مقابل خوردگی یا انجام آزمایش های مختلف خوردگی مانند آزمایش مه نمکی، آزمایش مقاومت به خراش یا چسبندگی و مقاومت به کندگی پوشش می باشد. به عنوان مثال پوشش گالوانیزه گرم بر اساس استاندارد ASTM A153 باید حداقل دارای ضخامت متوسط 50 میکرومتر بوده که این مقدار معادل مقاومت 400 ساعت در مقابل تست مه نمکی است اما هر یک میکرون ضخامت پوشش PTFE ، 100 ساعت در مقابل آزمایش خوردگی مه نمکی تحمل دارد و برای 400 ساعت مقاومت در برابر خوردگی ضخامت معادل 4 میکرومتر پوشش PTFE لازم است.
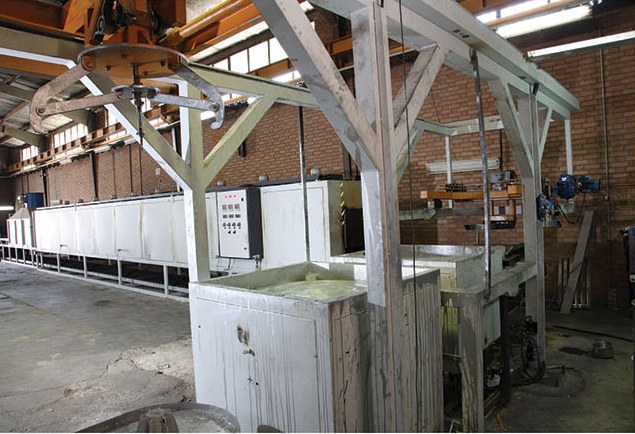
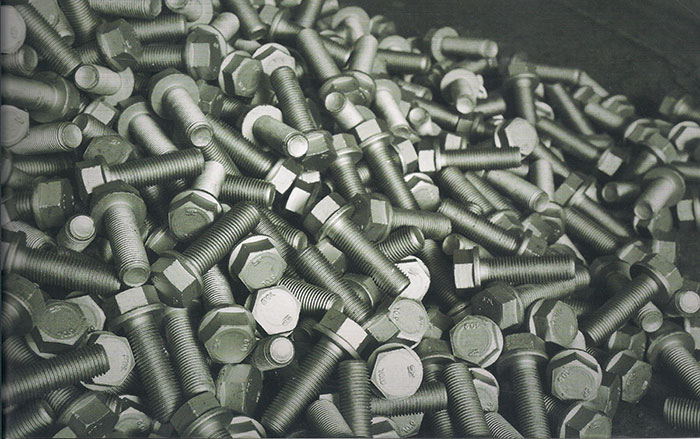